Lead & Co-Construction Project Manager | 50 Hudson Yards | Manhattan, NY
July 2019 - July 2022

​General Information & Project Scope
50 Hudson Yards is a 58-story, 981 feet tall commercial building that is the last to be constructed on the Main Hudson Yards Development Square. The building opened on October 20th, 2022, and ranks as the fourth largest office tower in New York City with 2.9 million square feet of usable commercial space. As published online, the total all in cost of the project neared $4.0B.
​
The superstructure is a unique blend of a concrete inner core with post-tensioned cable ties connecting it to a steel - metal deck -concrete slab outer core. Around 11,460 insulated glass unit panels, Italian sourced stone columns, and aluminum scoop panels enclose the exterior of the building. Two entire floors and the roof of the building are dedicated to extensive MEPS equipment which serve zones based on the Tenants needs. 50 Hudson Yards is the first tower in the U.S. to employ the TKE Twin Elevator system. Within 22 elevator shafts, each shaft has at least (2) elevators within it that speak to one another via an internal BMS like control. This increases the speed and efficiency of the elevators reaching their pick-up and drop-off destinations. Last major note, the sub levels of the building include some unique features that are paramount to the operation:
-
A vehicle valet lift and truck delivery lift that leads to an underground 360 degree vehicle carousel
-
Underground access tunnels to the other Hudson Yards buildings and MTA stations
-
Safeguards including "bank vault" like flood gates in case of flooding emergencies
​
The Construction Team consisted of Related Companies Upper Management and Project Managers | Project Engineers | Superintendents from my company. Based on criteria given to my company by Related Companies, individuals were suggested to Related, interviewed, and then selected if their calibre fit the project's needs. The overall blended team included 30+ individuals and unique challenges in terms of the pain-staking coordination required between the disciplines (i.e. Superstructure including built in/poured in/welded in facade support and facade building sway tolerances).
​
Role as a Lead & Co-Project Manager | Change Management
I was initially brought on to the project in 2019 to serve on the Related Change Management Team that oversaw changes touching each department and discipline. Sidebar: Before 50 Hudson Yards, I was considered for the Change Management Manager position overseeing the program within my company's NYC Business Unit, but it was concluded that my growth and exposure as a PM on 50 Hudson Yards would better serve my company and myself. The superstructure steel at this time was erected to the 5th floor and Facade-Superstructure coordination & start-up of Facade Manufacturing was at its heaviest. It was decided by Related that I was to join the Building Enclosure Team as a Co-PM | PE and transition into the Lead PM role for Roofing & Waterproofing. ​​​​​​​​​​​​​​​​​​​​​​​​
A
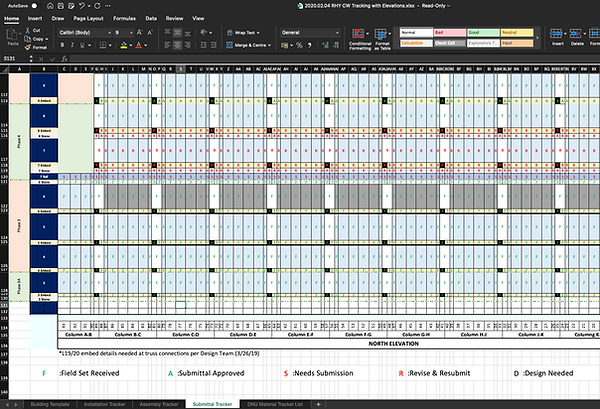
B

C

My priority responsibilities upon joining the Facade Team included:
-
Learn the submittal, fabrication, tracking, inspections, and installation process of the manufacturer, supplier, and installer and convert these findings into a highly detailed internal tracking system to be updated daily. This information shall also be able to be used or converted for presentation purposes at an Upper Management high level.
** Images A & B above show snippets of an Excel Tracker I created to visually represent statuses for Facade & Embed pieces
** If you are curious of just how detailed this Tracker gets, I invite you to click the "Facade Tracker.xlsx" link above
-
Establish a relationship with and set up at least once a week visits with the Delaware Assembly Plant and report back
-
Compile the facts and history to negotiate previous change orders and lead all Building Enclosure Change Management processes moving forward.
-
Lead the Facade Embed tracking and installation on site program. This included inspections with the 3rd Party embed testing agency
-
Bring data for, participate in, and follow through with marching orders for the once a week (half a day) Superstructure x Concrete x Facade design build coordination review. This exercise was truly a once in a lifetime experience. This Operational Triumph created synergy and accountability between all Management Teams and Trades involved, yielded cost and time savings considering many facade anchorage supports were re-designed to be pre-fabricated/welded on the steel before delivery, and prevented high risk welding/connection "gymnastics" that would not only slow on-site productivity, but create install safety hazards for work at the edge of each floor.
​
The processes described above I had to do to some extent (some more, some less) for the other Bid Packages I was prescribed to Lead as PM throughout the project's lifecycle. Yes, this included finding unique ways to manage cross discipline coordination, manufacturer visits, change order processes, daily coordination with internal Teams like the MEPS Team, unique reviews to solve or forecast risks that could be detrimental to the project, etc... These packages included Roofing & Waterproofing, Misc Metals, Painting, Flooring, and Misc Architectural.
​
​This project will forever be one of my top proudest achievements due to exponential growth it forced all of us to have and most importantly for showing myself that I have the capacity to learn with, take directive from, manage others within, and form "care for each other bonds" the 30+ member Project Management team.


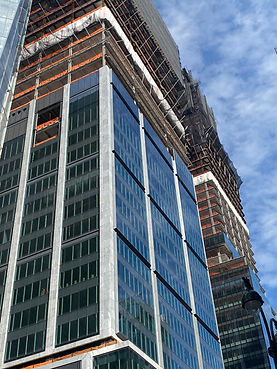